Adamas ha portato in Italia il software intelligente per l’ottimizzazione di picking e batching
Adamas, startup innovativa che applica l’intelligenza artificiale all’ottimizzazione logistica, ha recentemente lanciato in Italia il suo software di ottimizzazione del picking e del batching. “È noto che, nel bilancio del magazzino medio, il picking rappresenti di gran lunga la voce di costo più alta, arrivando spesso a toccare (e a superare) il 50-60% del totale. […]
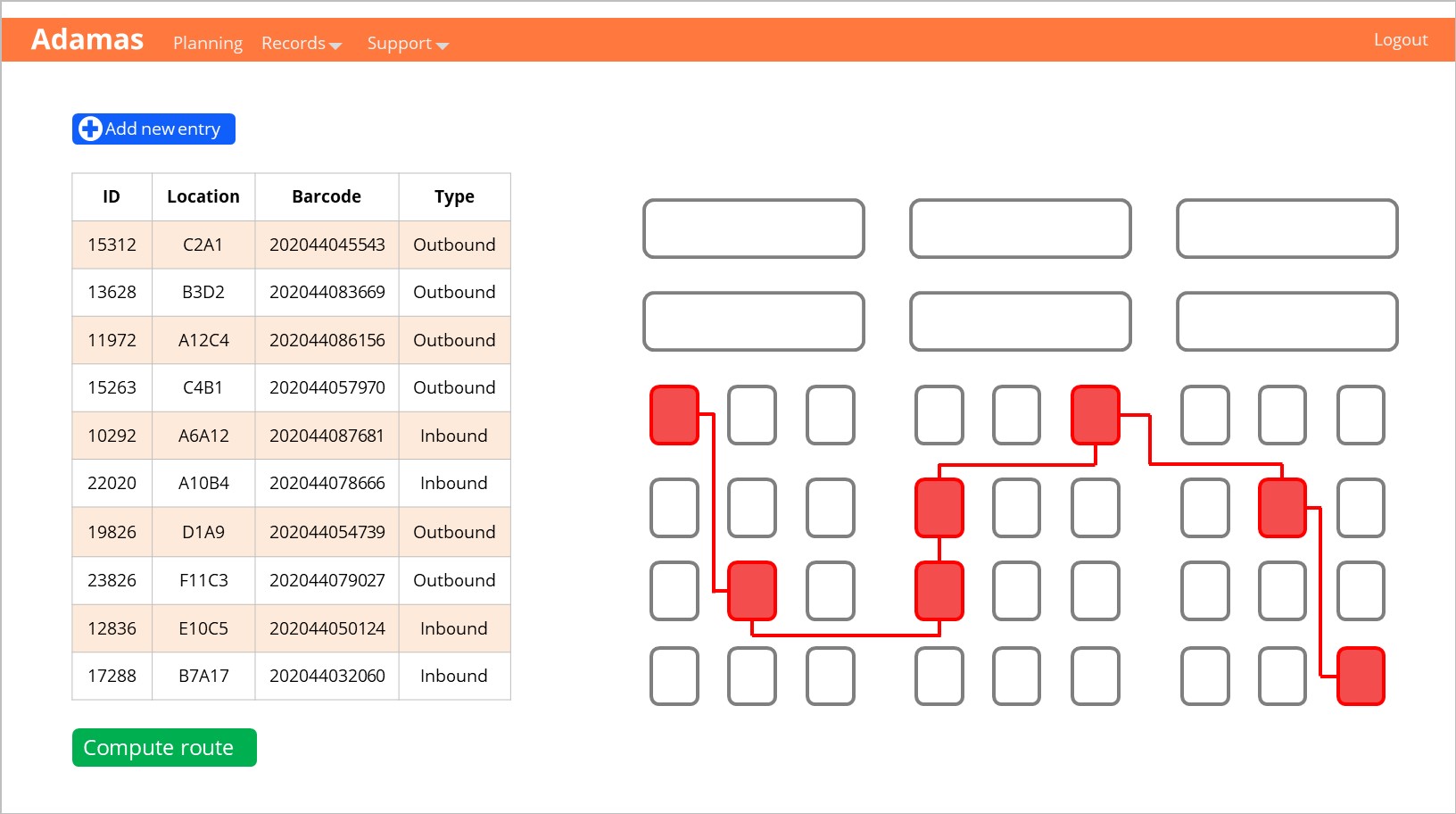
Adamas, startup innovativa che applica l’intelligenza artificiale all’ottimizzazione logistica, ha recentemente lanciato in Italia il suo software di ottimizzazione del picking e del batching.
“È noto che, nel bilancio del magazzino medio, il picking rappresenti di gran lunga la voce di costo più alta, arrivando spesso a toccare (e a superare) il 50-60% del totale. Nella maggior parte dei casi, la ragione dietro a costi tanto alti sono pratiche di picking inefficaci e superate” spiega l’azienda in una nota. “Le strategie di picking più popolari prevedono di visitare i vari corridoi seguendo uno schema geometrico fisso: il picking a S, in cui il corridoio viene percorso completamente, il picking a M, in cui il corridoio viene percorso solo fino all’altezza dell’ultimo oggetto che deve essere prelevato, e così via”.
Contrariamente all’opinione più diffusa, secondo Adamas questo tipo di metodologie di picking è inefficiente e finisce spesso per aumentare senza ragione la lunghezza totale del percorso. Percorsi di picking più lunghi corrispondono chiaramente a costi e tempi di evasione degli ordini più elevati.
Il software sviluppato da Adamas utilizza una strategia diversa, basata sull’analisi sistematica dei dati: per prima cosa, il programma analizza la piantina del magazzino e utilizza un algoritmo per creare un modello matematico dell’edificio. Da tale modello matematico il software “impara” a distinguere corridoi, scaffali e distanze tra i vari colli. Quando poi il personale specifica al software quali siano gli ordini che devono essere evasi e il contenuto di ciascuno, il software utilizza un secondo algoritmo che raggruppa gli ordini sulla base del loro contenuto e stabilisce quali di essi debbano essere raccolti nello stesso percorso di picking (processo definito batching), e poi calcola il percorso di picking più breve per ogni gruppo di ordini.
“Tale procedura rappresenta una grossa novità per i magazzini” sostiene ancora Adamas. “In primo luogo essa offre un’ottimizzazione su misura, basata sulla specifica configurazione dello stabile in cui viene applicata, delineando così un decisivo vantaggio qualitativo rispetto alle strategie fisse e generiche di picking geometrico. In secondo luogo la continua analisi dei dati consente al software di imparare dall’esperienza e di migliorare le proprie prestazioni nel tempo, a differenza dei classici approcci statici che applicano costantemente gli stessi percorsi di picking, a prescindere dalla loro efficacia. In terzo luogo l’ottimizzazione congiunta di picking e batching offre livelli di efficienza prima impensabili”. Nelle metodologie classiche di gestione il batching, quando effettuato, si riduce tipicamente a una suddivisione più o meno casuale degli ordini in diversi gruppi. La gestione di questo processo tramite una metodologia sistematica e rigorosa fondata sull’analisi dei dati permette di ridurre sensibilmente la lunghezza dei percorsi di picking, e con essa tempi e costi.
ISCRIVITI ALLA NEWSLETTER GRATUITA DI SUPPLY CHAIN ITALY