ISCRIVITI ALLA NEWSLETTER GRATUITA DI SUPPLY CHAIN ITALY
Alce Nero ha presentato il suo nuovo centro logistico realizzato con Toyota
Rimini – Alce Nero, azienda emiliana attiva nella vendita di una vasta gamma di prodotti provenienti da agricoltura biologica, in occasione dell’ultimo Richmond Logistics Forum appena andato in scena a Rimini ha alzato il velo, insieme a Toyota Material Handling Italia, sulla recente implementazione del proprio magazzino di Castel San Pietro (Bologna). Raffaele Santi, supply […]
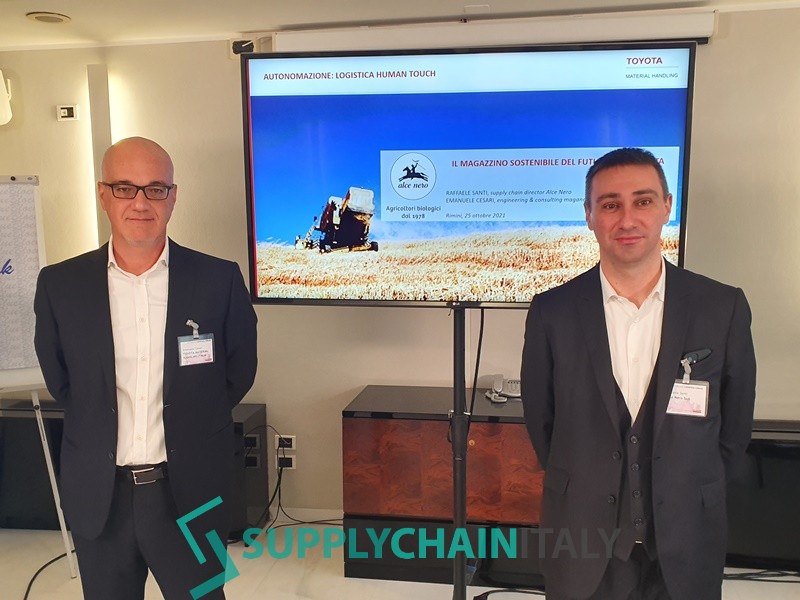
Rimini – Alce Nero, azienda emiliana attiva nella vendita di una vasta gamma di prodotti provenienti da agricoltura biologica, in occasione dell’ultimo Richmond Logistics Forum appena andato in scena a Rimini ha alzato il velo, insieme a Toyota Material Handling Italia, sulla recente implementazione del proprio magazzino di Castel San Pietro (Bologna). Raffaele Santi, supply chain director di Alce Nero, ed Emanuele Cesari, engineering & consulting manager di Toyota, hanno raccontato nel dettaglio quante e quali attrezzature e investimenti sono stati dedicati a questo struttura che sorge su una superficie di circa 15.000 mq (è stata raddoppiata nel 2019) e vede ogni anno transitare circa 400 prodotti diversi frutto dei raccolti e del lavoro di un migliaio di agricoltori italiani e circa 10mila imprese agricole del Centro-Sud America. I prodotti sono pasta, riso, passata e polpa di pomodoro, verdure, legumi e vellutate, frollini, succhi e nettari di frutta, composte e miele, bevande vegetali e una linea baby completamente dedicata alla prima infanzia. Ad essi si aggiungono la linea fresca, tra cui frutta, verdura, yogurt con e zuppe, surgelati, gelati e un biologico Fairtrade che proviene dai produttori latino americani (caffè, cioccolato, cacao, zucchero di canna, riso Basmati e tè).
Il “magazzino sostenibile del futuro” realizzato da Alce Nero con Toyota, dopo un’attenta fase di ascolto delle necessità, è stato studiato per movimentare “elevati volumi di beni prodotti una volta all’anno” ha precisato Santi, spiegando che dall’Italia Alce Nero “esporta in diverse parti del mondo, soprattutto Asia ed Europa centro-orientale”.
Cesari da parte sua ha evidenziato il concetto secondo cui “stare fermi oggi non è un’opzione”, aggiungendo che “la parte software è la vera customizzazione che oggi si può fare” per assistere un cliente nel ridisegno e nella implementazione del proprio magazzino.
Alce Nero ha voluto progettare e sviluppare un nuovo centro logistico sostenibile per ‘governare’ al meglio il suo mercato e le nuove opportunità. “Sfruttare Industria 4.0 come strumento di supporto all’investimento e non come risparmio fiscale, traguardare piani di crescita sostenibile con l’obiettivo di espandersi anche all’estero, cercare soluzioni sostenibili sia in termini economici che dal punto di vista ambientale, garantire la massima sicurezza sul luogo di lavoro e finanziare l’investimento mantenendo la certezza dei costi del noleggio”: queste le priorità alla base della scelta di investire sul restyling del proprio magazzino secondo il supply chain manager di Alce Nero.
Toyota Material Handling Italia da parte sua ha ricoperto il ruolo di unico integratore/fornitore per tutte le necessità intralogistiche e di material handling, rivolgendosi a fornitori terzi per quelle attrezzature non ‘di propria competenza’ ma rimanendo sempre il general contractor. La ricerca di opportunità di miglioramento è passata in primis attraverso l’eliminazione degli sprechi: “Quando si parla di Logistica 4.0 il modello non è solo l’automatizzazione ma quello dell’interconnessione; l’obiettivo non è eliminare il fattore umano ma cancellare o ridurre al massimo le funzioni più ripetitive” ha precisato Cesari.
Due gli obiettivi principali: in primis crescita della produttività aumentando l’efficienza e la sicurezza, ma anche piani di crescita a risorse ‘costanti’, ottimizzando lo svolgimento delle attività attraverso un efficientamento dei processi.
Questi invece i driver strategici individuati: implementazione delle logiche del sistema automatico unite alla flessibilità delle persone, ottenendo un sistema flessibile e riconfigurabile; mantenere il numero di risorse (personale diretto) costante facendo loro eseguire attività a valore aggiunto, tracciabilità completa delle merci e delle movimentazioni.
Fra le innovazioni hanno trovato posto tre navette Radio Shuttle per circa 1.600 posti pallet e la seguente flotta di 24 carrelli:
3 Retrattili RRE160H per stoccaggio/abbassamenti e riposizionamenti
1 Retrattile RRE160M per movimentazione magazzino a cataste
4 Transpallet con pedana LPE250 per carico/scarico camion su 17 baie di carico
3 Stoccatori con pedana SPE200D supporto a navettaggio, picking e fascia pallet
11 Commissionatori OSE120CB per picking con sistema T_Mote «Stop & Go»
1 Carrello frontale 8FBEK18T movimentazione in piazzale e magazzino cataste
1 Stoccatore HWE100 in uso al magazzino e-commerce
Nel rinnovato centro logistico hanno trovato spazio anche 10 postazioni di ricarica i_battery per il funzionamento dei 19 carrelli. In termini di attrezzature sono state fornite e installate una scaffalatura porta –pallet, radio shuttle, un magazzino autoportante refrigerato e un magazzino verticale.
Questi sono alcuni dei risultati ottenuti elencati da Raffaele Santi ed Emanuele Cesari: un abbattimento degli errori operativi, il massimo sfruttamento del magazzino, una riduzione dei tempi di movimentazioni, dei percorsi dei mezzi e del numero di carrelli necessari, un incremento delle missioni svolte giornalmente, una riduzione dei costi di manutenzione, rintracciabilità puntuale della merce, nessuna perdita di tempo per lettura dei codici e dunque ottimizzazione del tempo degli operatori.